You Know About Of Different Types Of Prefab Homes
- annawrench1315
- Jul 2, 2020
- 3 min read
Updated: Sep 13, 2023
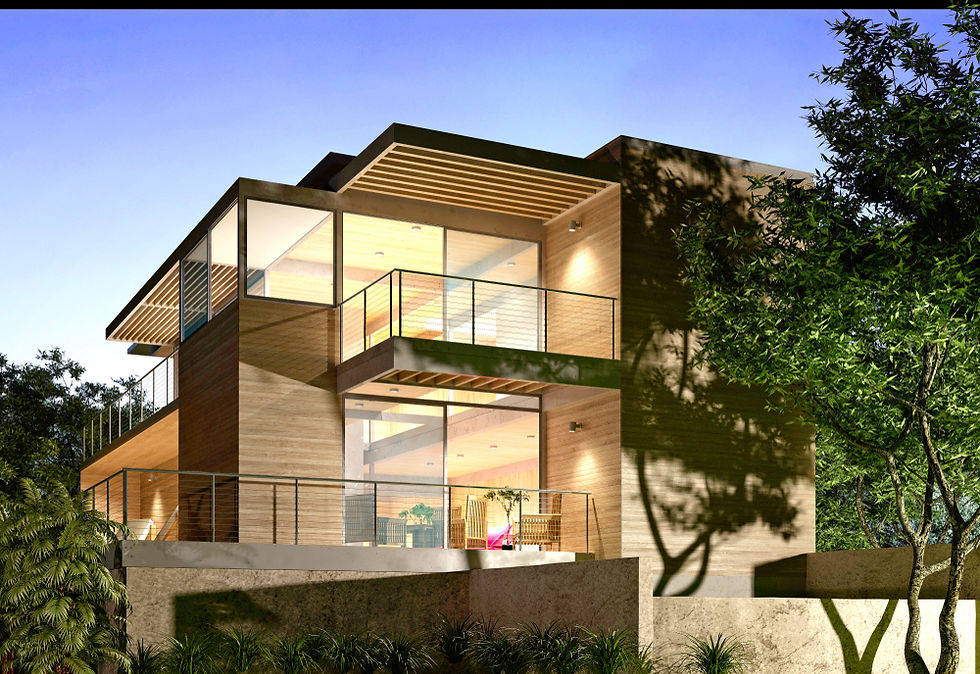
Gone are the days when prefabricated homes were considered temporary, fragile and cardboard-like. Present-day prefab homes are downright magnificent. They not only provide you an energy-efficient, custom-built solution, but they are also more cost-effective than traditional concrete homes. While the cost of such homes largely depends on their size, location, and amenities in it, you can save a lot of time and money by having them made.
Essentially, prefabricated homes are the structures that are manufactured in a factory setting and then shipped to your building site in panels. Finally, these panels are assembled on your site within a few days. Since these homes meet the building codes just like the concrete structures, they can be built almost anywhere. Apart from that, just like concrete homes, prefabricated homes also qualify for home loans which means that you can have them even if you don’t have ready money in hand. Some manufacturers also help you find financing, and some even offer in-house financing to start the construction of your house. But before you make up your mind, find out the different types of prefab homes you can choose from.
Types Of Prefab Homes
Modular Home: This type of prefab homes consists of a couple of modules that are constructed in a factory as per the local and state building codes. Then they are separately transported to your building site and assembled there to complete the construction. Most of these modules also contain interior fittings, including the stairs, closets, doors, electrical and plumbing systems, etc. So, there is almost no finishing work required to assemble such homes. Depending on the size and amenities of the house, you are ready to move in as little as 3-6 months after placing your order.
Pre-Cut Home: Also known as dome homes or kit homes, these homes are designed and cut in the factory and shipped to the building site as a complete kit. Some of them are panelized homes, but all panelized homes are not pre-cut homes. Most of these homes are designed for buyers who want to construct their homes on their own using the instructions and materials provided by the manufacturer. Detailed instructions and all the needed parts are provided by the manufacturer in these kits. The home buyers can piece the kit together either on their own or with the help of a professional contractor. The major difference between a modular home and a pre-cut home is that modular homes are constructed in factories and assembled at the building site, but with a pre-cut home, the manufacturer’s duty finishes as soon as they deliver the designed kit to your site. They are not responsible for assembling these prefab homes.
Panelized Home: These homes are in-built panels that are transported to the building site and assembled to make a new home. Typically, more finishing work is required in these homes as compared to other types. For example, painting and installation of flooring, stairs, and cabinets have to be done on-site. Assembling this type of prefab home takes more time than others, and you may need the help of professional contractors as well to get the job done with perfection.
Shipping Container Home: These homes are like shipping containers that can be pieced and stacked together to make residential and commercial spaces. These are strong and sturdy, but they are not that great for residential purposes, as your state may have restrictions for the construction of these containers as homes.
Now that you know the different types of prefab homes, it’s up to you to choose the one that best suits your requirements, preferences, and budget. Check the quality of the homes and reputation of the manufacturer before making the final decision.
Comments